Our Platform
At 3DBioFibR, our mission is to lead the global production of nature’s strongest, lightest, and toughest materials, solving critical engineering challenges of our communities.
Technology
Our patented dry-spinning technology produces protein fibers at scale, that closely mimic the structure, biochemistry, and biomechanics of their natural counterparts. Our fully automated system for CollaFibR® production uses GMP inputs to ensure consistent fabrication at commercial scales.
We have commercially available products for 3D bioprinting and cell culture and can also create custom non-woven collagen scaffolds for tissue engineering.
With over 1000X the throughput of competing technologies, our dry-spinning approach is the first to spin collagen fibers at commercial scales.
By recreating the extensional flows that drive natural self-assembly processes, our fibers closely replicate the structure, biomechanics, and biochemical properties of natural collagen structures.

Beyond Collagen
While our main focus is on collagen fiber manufacturing, we have successfully spun various network forming biopolymers, including spider silk, fibrin, and chitosan.
SpidrFibR™: an extraordinary spider silk prototype with limitless possibilities. Five times stronger than steel and more extensible than rubber, spider silk is a marvel of nature. Scientists have long sought to replicate its remarkable properties, and now, with the use of our patented technology, SpidrFibR™ has doubled the record for recombinant spider silk tensile strength. This groundbreaking material holds immense potential in applications ranging from green textiles to aerospace engineering and defense. For further information on SpidrFibR™, detailed data is available for discussion under a CDA.
3DBioFibR is led by an experienced team with scientific, industry and business leadership experience.
Founders
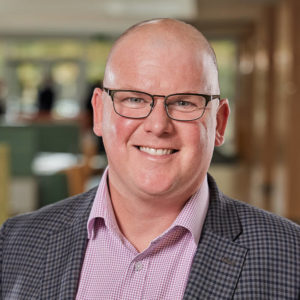
Kevin Sullivan, CEO
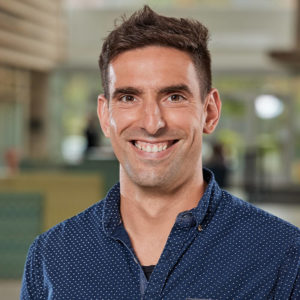
Dr. John Frampton, CSO
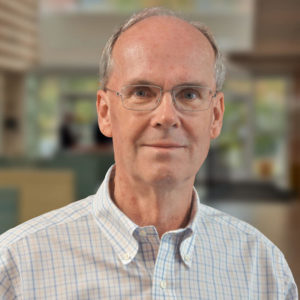
Craig gauld – VP
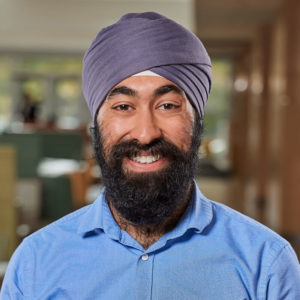
Gurkaran Chowdhry, Director of Business Development
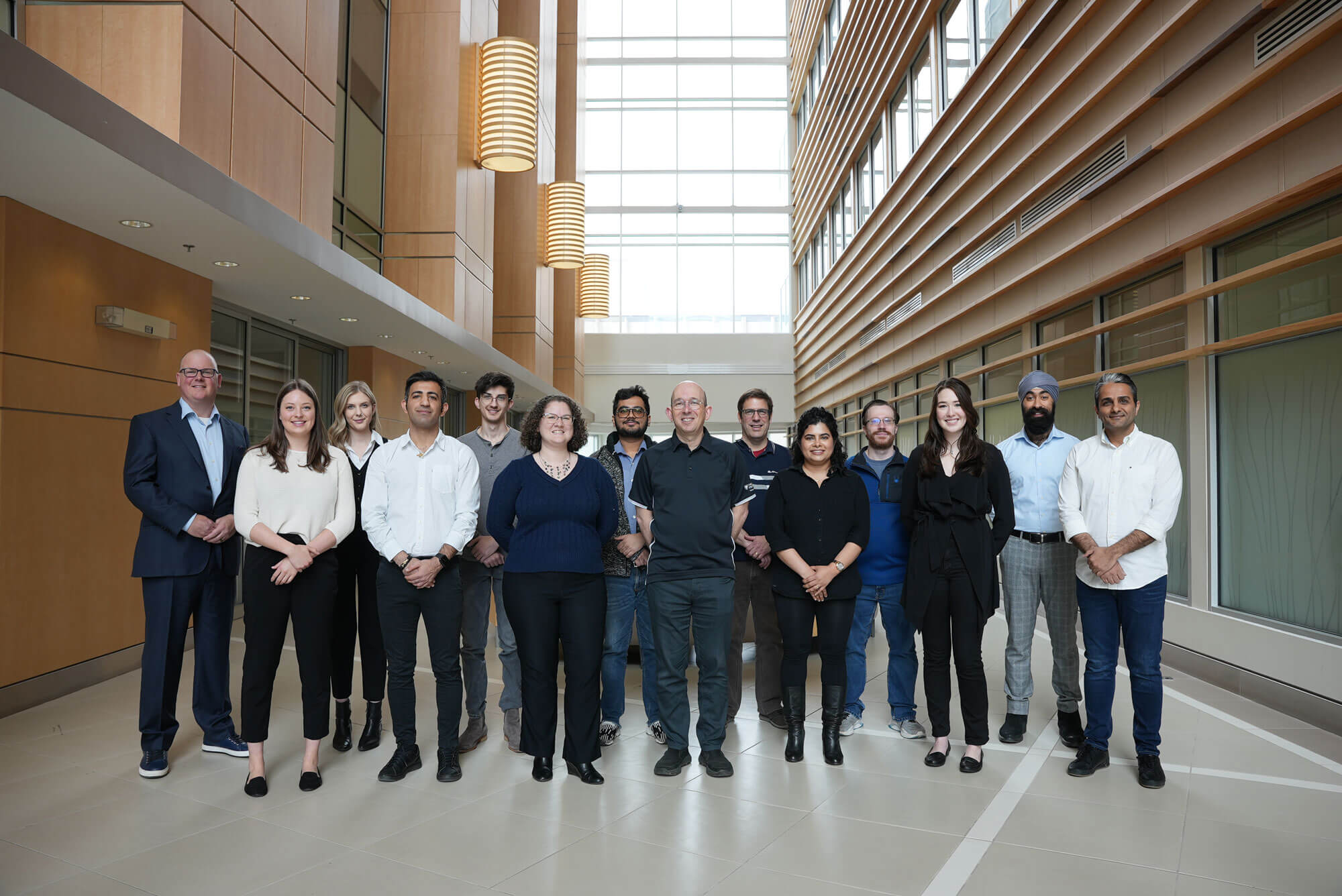